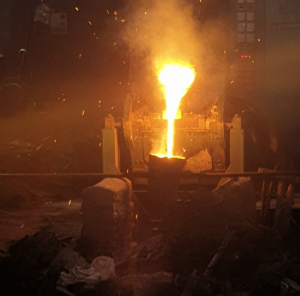
Industry Visited: | Metals cast Pvt. Ltd. Butwal Industrial District, Butwal, Rupendehi |
Date: | 16th August 2019 |
Transportation: | Local Bus |
Participants: | 4 |
Metals cast is a foundry serving Nepalese Industries for their requirement of casting and fabrication of various metals. Metals cast produces components of Ferrous Alloys, Copper alloys and Aluminum through green sand molding processes. Metals casts was established in 2049 B.S. It started as a jobbing foundry with focus on requirements of industries in and around Butwal. Metals cast has the advantage of successfully producing thousand type of products to customer satisfaction which makes it versatile in producing a wide range of customer requirement, however complex it may be.
It has the capacity of producing up to 25,000 Molten Steel per day and up to 2500 Kg single casting of ferrous alloys and copper alloys.
Ground Report
After consulting with Metals cast PVT. LTD, August 16th was the day for visit. We planned to travel on August 15th from the university. For transportation, local bus were used. The bus departed from Kathmandu valley at 8:00 am. We arrived at Butwal at 9:00 pm, and stayed at a hotel. The visit was scheduled for the next day at 10:00 am. Mr. Nischal Sharma picked us at 9:30 am. We were then introduced to the faculty and workers there. After safety briefing and putting on the safety gears, we were then taken to the plant. Mr. Sharma started with the post machining machine which includes lathe, CNC lathe, Sand blaster, grinding wheel, Milling, welding, and heat treatment plant. He explain the procedures of these machines and when they are used. Then he took us to the casting furnace. The industry currently have 3 furnace, two of which are currently running and the one is being constructed. There is a smaller furnace of which requires 450kW of power and a capacity of 250kg. The medium one requires 750kW of power and a capacity of 1tonne. The one being constructed requires 1MW of electricity. He explains the basic of the furnace and how they change the material for different types of casting. For the 750kW furnace, the crucible is lifted via crane. After a brief introduction to everyone and every components of the factory, we then observed the casting process there. We observe how the cope and drag are made based on the complexity parts to be casted. Also were the gas vent, runner and riser are to be located and their areas. After closely observing 4 to 5 sample of crusher plate casting, we started to work on casting of a section of Francis Turbine Runner.
As wholesome section of blade was rather difficult to produce in sand casting to retain its structure, We decided to divide the blade into two parts. One with blade and shroud section and the other with hub section. We made the cope and drag and runner and gas vent was made with the help of the experts there. After completion of the mold, cope and drag were blasted with air to clear the debris and then heated with a blow torch.
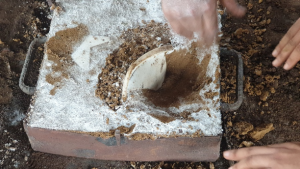
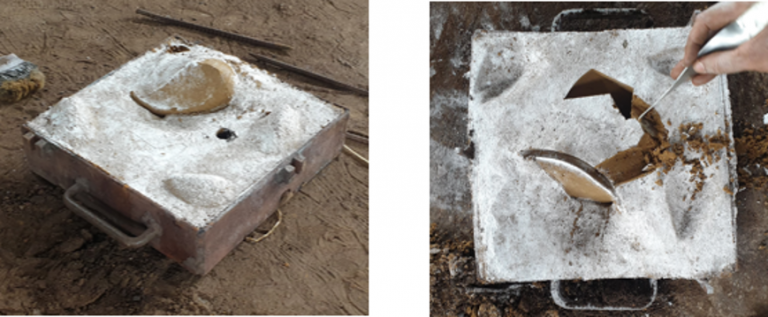
After this we went for a lunch break. After lunch as we returned, the smaller furnace was in preparation for casting. We locked the mold and seal it with clay.
When the molten metal was ready to be poured, the area was cleared and the experts at Metals cast poured the molten metal on the mold.
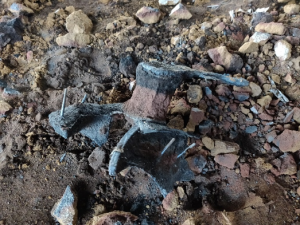
Since we were running out of time, the section of runner was allowed to cool down for 20 mins and the mold was broken. The hot section was then blasted with water to cool and then blasted with sand blaster. Necessary grinding was followed then after. The runner and gas vent were cut off and additional grinding was done.
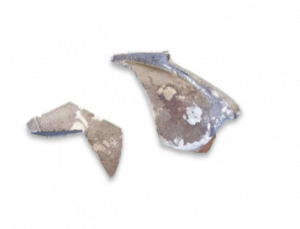
The section was as good as the 3D-printed model. After this only welding of the parts were to be done which was carried out here at Kathmandu University.
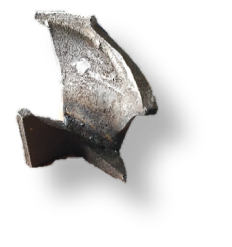
We also visited laboratory of Metals casts which comprised of various equipment and machines for testing facilities including hardness testing, spectrometer for cavity testing etc.
Participants review about the visit
Abishek Kafle Research Assistant | Visit to Metals cast gave us a wonderful exposure to industrial working environment of Nepal. Seeing level of work out there motivate as well as challenged me as a researcher to come up with new and innovative ideas in the area of casting and manufacturing in Nepal. We are thankful to the Metals cast team for being so welcoming and providing us a wonderful environment to work for the whole day in the factory. |
Prashil Raj Shrestha BE in Mechanical Engineering | It was a wonderful experience to visit Metals cast Pvt. Ltd. We gained a chance to merge our theoretical knowledge with practical skills. We also get the exposure to how a manufacturing company works. We were briefed about the safety and rules about the plant. We were taken through Raw Material Storage units, post machining unit, casting unit, testing unit, etc. Surely this visit will be very important for our project as we can validate it with our simulations. |
Smrit Dhimal BE in Mechanical Engineering | Engineering Visit to Metals cast was a good experience which provided us exposure to casting process linking theoretical knowledge and practical. This visit improved our knowledge of the casting process and regarding our understanding of how to design gating system. We got chance to observe the casting of various parts of various materials. The hands-on experience of mold making and casting the blade will surely help us optimize our design for simulation. So, it was a very fruitful experience. I am sure this visit will help us in our final year project. |
Navin KC BE in Mechanical Engineering | Our visit to Metals cast was a fruitful as well as great experience for us and helped us in a plethora of way. Since, our project had been related to casting, it helped us develop some depth insights about the Casting process through the experienced workers and laborers. The experience was truly inexplicable as we got watch the full process form the melt to full product where we got experience development of gating system, mold preparation and so on. Hence, the visit was a success for our project to understand the vital components in viewing the simulation to make it as error proof as possible. |